厂商 :广东思豪内高压科技有限公司
广东 佛山市- 主营产品:
- 内高压成形机
- 门板压花机
- 水胀液压机
联系电话 :13378470538
商品详细描述
管材内高压成型设备
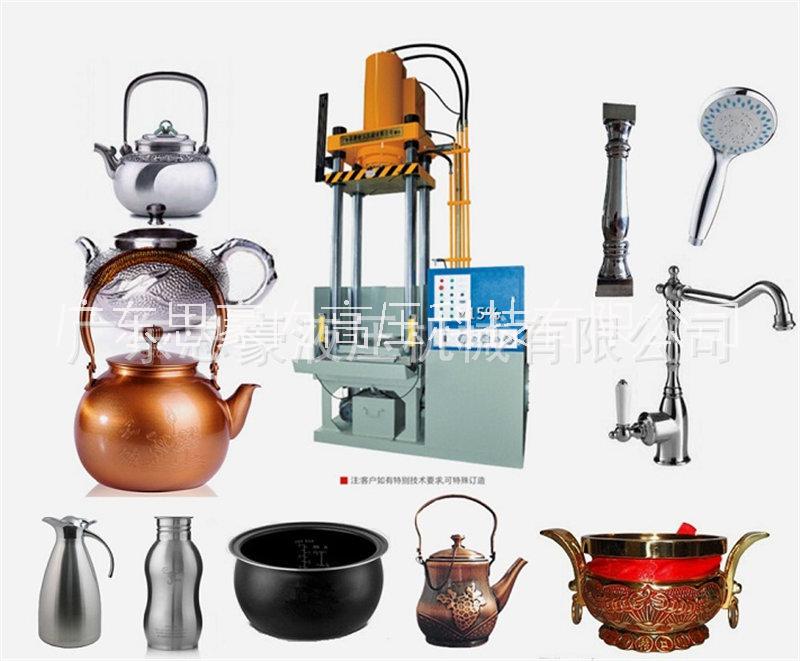
内高压成形技术的原理及分类
内高压成形技术研究与应用新进展: 概念:管材液压成形为内高压成形 内高压成形(Internal High Pressure Forming)是以不锈钢、铜、铁、铝、等复合材料管材作坯料,通过管材
内部施加高压液体和轴向补料把管材压入到模具型腔使其成形为所需形状的工件。利用乳化液体作为传力介质或
模具使工件成形的一种塑性加工技术(在水中添加少量的防腐剂等组成)作为水传力介质,又称为管材液压成形
(Tube Hydroforming)也称为液力成形。
介绍思豪液压近年来在内高压成形件及在汽车、航天、航空中的应用。理、工艺、设备和应用方面的最新进展。
空心异形截面零件,液压成形技术同冲压,焊接等传统的成形技术相比,是一门新型的金属成形技术。 按使用的液体介质不同,液压成形分为水压成型和油压成型;按使用的配料不同,液压成形分为管材液压成形,
板料液压成形和壳体液压成形为了解决汽车,航空航天等领域的一些复杂的工艺问题和技术要求针对大截面差管件,弯曲轴线异型截面构件和枝杈管3类工艺,给出典型零件缺陷形式、形状精度、壁厚分布和工艺参数的影响。详细介绍了皱纹控制与利用,降低整形压力的方法和内压与轴向力耦合作用下管材的塑性失稳起皱分析。最后给出了研制的典型 (2)液体具有实时可控性 种类 种类 介质 最大成形压力 板料液压成形 液压油 不超过100MPa壳体液 壳体液压成形 纯水 不超过50MPa 管材液压成形 多为乳化液 不超过400MPa 液压成形的特点: 1、液体作为传力介质具有实时可控性,通过液压闭环伺服系统和计算机控制系统可以按给定的曲线精确控制
压力,确保工艺参数在设定的数值内,并且随时间可变可调,大大提高了工艺柔性。 2、液压成形技术仅需要凸模和凹模中的一个,一次1-5件,或者不使用任何模具,这样可以省去一半,甚至
不需要花费制造模具的费用和加工时间,而且液体作为凸模可以成形很多刚性凸模无法成形的复杂零件。 内高压成形技术的原理及分类: 内高压成形设备和模具 内高压成形机由液压泵站、水压系统、合模压力机、电器系统、增压缸六部分组成。 工作过程:模具闭合—主缸下压合模力—对管材内填充加压介质—管端密封—按加载曲线施加内压和轴向进给
—充水增压整形—成型后卸压—拔模力—退回冲头—开模 1、成形技术分类: 薄壁多通管内高压成形技术: 不锈钢卡压管件包括有T形三通管、Y形 L形管、X形四通管和六通管等,按照壁厚大小,可以做到壁厚
0.5mm~ 2.5mm的不锈钢管件、铜管件。T型和Y型三通管件是多通管中应用最多的产品。其原理是向管内充
满液体,并施加一定的水胀压力,然后左右冲头施加轴向力补料和送料,同时中间的冲头退回,最终形成所需零件。内高压水胀技术解决了三通管件的传统半管焊接和插焊工艺。
2、内高压成形特点 多通管件的成形工艺过程分为3个步骤 ①成形第一阶段,中间冲头不动,左右冲头进行轴向补料的同时,向管材内施加一定的内压,支管顶部尚未接触中间冲头,处于自由胀形状态。 ②成形第二阶段,从支管顶部与中间冲头接触开始,内压继续增加,按照给定的内压与三个冲头匹配的曲线,
左右冲头继续进给补料,中间冲头开始后退,后退中要保持与支管顶部接触,并对支管顶部施加一定的反推力
,以防止支管顶部的过度减薄造成开裂。 ③成形第三阶段,左右冲头停止挤压,中间冲头停止后退,迅速增加内压进行整形使支管顶部过渡凸区我范围
达到产品和模具设计要求 按使用坯料不同: 大体可分为管材液压成形、板材液压成形、壳体液压成形。 板材液压充液成形技术: 板材液压成形是利用液体作为传力介质来传递载荷,使板材成形到单侧模具上的一种板材成形方法,根据液体
介质取代凹模或凸模可将之进一步分类为充液拉深成形和液体凸模拉深成形。 适用范围:适用于筒形、锥形、抛物线形盒形领域的等变形程度超过普通拉深成形极限的板材零件,例如航天
领域整流罩、头套以及汽车领域的发动机等覆盖件。 优点:提高成形极限和减少成形道次。
弯曲轴线变截面管件内高压成形: 弯曲轴线管件内高压成形工艺过程包括弯曲、预成形、内高压成形等主要工序。由于构件的轴线为二维或三维的
曲线,需要先经过弯曲工序,将管材弯曲成和零件轴线相同或相近的形状。为了确保管材能顺利放到模具内,
弯曲后一般要进行预成形。(图为一个铝合金变截面管件,其成形过程为弯曲-预成形-内高压成形,
以获得各个不同位置的多个截面形状,其最大减薄率为7.5%) 壳体液压成形: 采用水作为壳体液压成形的传力介质具有成本低和清洁等优点,但对于 大容积壳体(1000m3 以上),水的质量
很大,壳体的支撑难度大,限制了给技术的进一步应用。是采用一定形状的封闭多面壳体作为预成形坯,在封闭多
面壳体充满液体后, 通过液体介质在封闭多面壳体内加压,在内压作用下壳体产生塑性变形而逐渐趋向于最终的
壳体形状。最终壳体形状可以是球形,椭圆,环壳等。(二氧化碳储罐材料为16MnR其中16Mn为低合金代号R
为代表容器类材料。) 对于单曲率壳体, 该工艺的主要工序为:下料—弯卷—组装焊接—液压成形 成形工艺:先由平板经过焊接形成封闭多面壳体,然后在封闭多面体内充满液体介质(一般为水), 并通过
一定加压系统施加压力,在内压作用下壳体产生塑性变形而逐渐趋向于球壳 优点:1)不需要模具和压力机。(产品初期投资少,因而可见底成本,生产周期) 2)容易变更壳体壁厚和直径。 3)产品精度高。(传统成形为先成形后焊接,焊接变形难以控制)
3、结构特点: 内高压成型机总体结构先进,紧凑,可靠,维护方便,操作简单。该内高压成型机由管胚本体机构、液压系统、
供水系统、控制台等组成。系统中元器件均采用实际工业元件,质量可靠、性能稳定,故障率低。该实训 设备的
生产、装配、服务等通过ISO9001质量管理体系认证 从工艺技术角度,内高压成形与冲压焊接工艺相对比的主要优点: 1) 提高强度和刚度,尤其是疲劳强度。 2) 材料利用率高。 (达到90%-95%) 3) 降低生产成本。(费用平均降低 15%-20%,模具费用降低20%-30%) 4) 减轻质量,节约材料。 ( 框、梁类 减轻20%-40%,空心轴可以减轻40%-50%) 5) 减少零件和模具重量,降低模具费用。 6) 可减少后续机械加工和组装焊接量,提高生产效率。 2.液压成形技术发展趋势 内高压成形技术: 1.超高压成形 2.新成形工艺 3.超高强度钢成形 4.热态内压成形板料液压成型技术: 1.大型复杂型面零件成形 2.与普通拉深工艺复合,提高效率。 3.提高成形极限和零件质量的成形新技术 4.低塑性材料的拉深成形
随着航天、汽车、航空和机械行业对结构整体化和轻量化的需求越来越高,液压成形技术尤其是内高压成形技术
在我国得到了迅速发展,逐渐成为工业生产中制造复杂异型截面轻体构件的一种先进成形技术。
相关产品推荐
-
佛山厂家标准拉伸机,500吨四柱拉伸油压机,非标定做 标准拉伸机非标拉伸机
-
供应用于拉伸成型机的佛山拉伸机 四柱液压油压拉伸机 800吨四柱液压油压拉伸机 五金
-
304不锈钢管件 医院给水工程食品级三通 不锈钢三通 厂家批发 不锈钢卡压件
-
供应水涨管件内高压液压机 水涨管成油压机
-
国内多功能定制水管航天汽车轻量化热门 内高压不锈钢卡压式管件内高成形机
-
铜管件内高压成形机卫浴空调供暖厂家国内制造设备水管铜管内高压水涨成形机
-
生产高精尖厂家供应民用汽车零部件内高压一体水胀成形机 汽车零部件内高压成形机 汽车 零部件内高压成形机
-
300T拉伸油压机 五金制品厂专用拉伸设备 佛山拉伸机厂家
-
云南火锅拉伸液压机 拉伸机 四柱成形液压机 Y28拉伸机
-
佛山200吨框架整形油压机 游戏币徽章成型设备