厂商 :深圳市伟烽恒科技有限公司
广东 深圳市- 主营产品:
- 无线射频芯片
- 压力传感器
- 无线模组
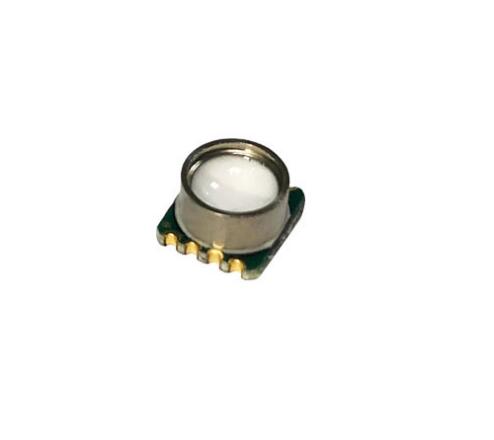
Digital Barometer Rev. 1.0 Key parameters ? Pressure range:300 … 1100hPa ? Package: 4-pin LGA metal-lid Footprint: 4.5 × 4.5mmP 2P Height: 3.5mm ? Relative accuracy: ±0.03 hPa(±0.25m) ? Absolute accuracy: typ. ±1.5hPa ? Temperature coefficient offset: 1.5 Pa/K, (12.6 cm/K) ? Digital interface: IP 2PC/SPI ? Current consumption: 3.5μA @1Hz sampling rate ? Temperature range: -40~+85°C ? RoHs compliant, halogen-free Typical applications ? Barometer and altimeter for portable devices ? Indoor and outdoor navigation ? Weather station equipment ? Sport watches ? Flying toys Technical advantages ? Wide compensate temperature -10~+80°C ? Small package, height only 3.3mm ? Excellent performance and cost Brief Description is a high precision barometer and altimeter especially designed for consumer applications. It measures the pressure based on piezo-resistive MEMS pressure sensor. The ultra-low power, low voltage electronics of the is optimized for use in mobile phones, smart watches, PDAs, GPS navigation devices and outdoor equipment. The sensor module is housed in a compact 8-pin metal-lid LGA package with a footprint of only 4.5 × 4.5 mmP 2P and 3.5 mm package height. Its small dimensions and its low power consumption allow the implementation in battery driven devices. With a low altitude noise of merely 0.08m and very low offset temperature coefficient(TCO), the offers superior performance and cost are perfectly suitable for applications like flying toys and sport watches. The IP2PC/SPI interface allows for easy system integration with a microcontroller. WF5805F WF5805F WF5805F WF5805F Tel: +86-755- E-mail: 23311175 sales@weifengheng.com http://www.weifengheng.com Rev. 1.0 1 Specification VDD = 3.3V, T=25°C, unless otherwise noted. Table 1 Parameter specification Parameter Symbol Condition Min Typ Max Units Operating temperature range TBA B operational -40 25 +85 °C full accuracy 0 65 Operating pressure range P full accuracy 300 1100 hPa Sensor supply voltage VBDD B 1.8 3.6 V Interface supply voltage VBDDIO B 1.8 3.6 V Supply current IBDD,LPB 1Hz, ultra low power 3.4 μA Peak current IBpeakB during pressure measurement 1950 μA Current at temperature measurement IBDDT B 900 μA Sleep current IBDDSL B 25°C 0.1 0.3 μA Relative accuracy VDD=3.3V ABrelB 700…900hPa 25…40°C ±0.03 hPa ±0.25 m Offset temperature coefficient TCO 900hPa 25…40°C ±1.5 Pa/K ±12.6 cm/K Absolute accuracy pressure 300…1100hPa -20…0°C ±2.0 hPa 300...1100hPa 0…60℃ ±1.5 hPa Resolution of output data in ultra high resolution mode Pressure 0.025 Pa Temperature 0.01 °C Noise in pressure VBP,full B Full bandwidth, ultra high resolution 1 Pa 8 cm VBP,filtered B Lowest bandwidth, ultra high resolution 0.2 Pa 1.7 cm Absolute accuracy temperature AP TP @25℃ ±0.5 °C 0…+65℃ ±1.0 °C PSRR (DC) PSSR Full VBDD B range ±0.005 Pa/mV Long term stability ΔPstab 12 months TBD hPa Solder drifts -0.5 +2 hPa Possible sampling rate fBsample B 587 649 TBD Hz WF5805F Tel: +86-755- E-mail: 23311175 sales@weifengheng.com http://www.weifengheng.com 60…80 °C Rev. 1.0 2 Absolute maximum ratings Table 2 Absolute maximum ratings Parameter Symbol Condition Min Max Units Supply voltage VBDDB -0.3 +3.6 V Voltage at all IO Pins VBDDIOB all pins -0.3 VBDDB +0.3 V Overpressure P 0 10,000 hPa Storage temperature TBSTORB -45 +85 °C ESD rating ESD HBM ±2 kV WF5805F Tel: +86-755- E-mail: 23311175 sales@weifengheng.com http://www.weifengheng.com Rev. 1.0 3 Operation 3.1 Brief description The is designed to be connected directly to an external microcontroller of a mobile device via the IP2PC or SPI bus. The pressure and temperature data has to be compensated by the calibration data of the on-chip Non-Volatile Memory (NVM) which is individually factory calibrated for each device. 3.2 Function description The consists of a piezo-resistive micro-machined pressure sensor, an analog to digital converter and a control unit with Non-Volatile Memory (NVM) and a serial IP 2PC/SPI interface. The delivers the uncompensated values of the pressure and the temperature. The individual calibration data are stored in NVM. This is used to compensate sensitivity, offset, temperature dependence and other parameters of the sensor. Figure 1 Block diagram of 3.3 Measurement of pressure and temperature The microcontroller sends IP2PC/SPI write register to start a pressure or temperature measurement. After converting time or checking status via the IP2PC/SPI, the result value (raw pressure data and raw temperature data) can be read via the IP2PC/SPI interface. For pressure and temperature calibration calculation in microcontroller, the calibration data in NVM has to be used. The constants can be read out from the ’s NVM via the IP2PC/SPI interface at software initialization. Temperature Sensor Temperature Sensor MUX PGA ADC Filter &DSP Serial Inter- face Control Logic OSC & Timing POR OTP Voltage Regulators I2C/SPI VDDIO VDD WF5805F WF5805F WF5805F WF5805F WF5805F WF5805F Tel: +86-755- E-mail: 23311175 sales@weifengheng.com http://www.weifengheng.com Rev. 1.0 Figure 2 Measurement flow of 3.4 Timing of the measurements The output data rate (ODR) of the measurements is controlled by the external microcontroller. A single measurement is performed according to the received IP2PC/SPI register value. When the measurement is finished, the sensor returns to sleep mode and the measurement results can be obtained via IP2PC/SPI interface. The ODR can be increased to more than 500 samples per second for dynamic measurement. For application with high ODR, constant tBdelay B is recommended as the (depends on mode) WF5805F WF5805F Tel: +86-755- E-mail: 23311175 sales@weifengheng.com http://www.weifengheng.com Rev. 1.0 self-heating of the pressure sensor and heat dissipation are in the balance if sampling rate is constant, which helps reducing the noise caused by irregular heat exchange between the sensor and the ambient environment. The recommended working timing diagram is shown in Figure 3. Figure 3 Recommended working timing diagram For applications which require low ODR or host-based synchronization, the tBdelay Bcan be set with any value larger than 0.5ms. The optimum compromise between power consumption, speed and resolution can be selected. 3.5 Measurement time The temperature and pressure measurement time depends on oversampling setting osr_t and osr_p. The following table shows the typical and maximum measurement time based on selected oversampling setting. The minimum achievable frequency is determined by the maximum measurement time. Table 3 Measurement time OSR setting (Single pressure or temperature) Measurement time [ms] Measurement rate [Hz] Typ Typ 256x 1.54 649 512x 1.86 537 1024x 2.5 400 2048x 3.78 264 WF5805F Tel: +86-755- E-mail: 23311175 sales@weifengheng.com http://www.weifengheng.com Rev. 1.0 4096x 6.34 157 8192x 11.46 87 16384x 21.7 46 32768x 42.18 23 3.6 Output compensation The output consists of the ADC output values include raw temperature and pressure data. Due to different characteristic of each sensing element, the actual pressure and temperature must be calculated using a set of calibration coefficients. These coefficients are individually factory calibrated and stored in the NVM. The NVM is organized with 16-bit data type. 3.7 Compensation formula The ODR and OSR can be selected by selected by the oversampling_setting in the C code. Using the driver C code provided by Inc. is strongly recommended. Please contact with Inc. for details. WF5805F WF Tech. WF Tech. WF5805F Tel: +86-755- E-mail: 23311175 sales@weifengheng.com http://www.weifengheng.com Rev. 1.0 4 Registers All the registers can be departed into normal registers and OTP registers. The normal registers are used to send a conversion command to the , read back the conversion data and perform the OTP blowing. The OTP registers are used to store the configurations and calibration coefficients for the , whose default values can be programmed by the inside OTP banks. 4.1 Normal Registers The is designed to be connected directly to an external microcontroller of a mobile device via the IP2PC or SPI bus. The pressure and temperature data has to be compensated by the calibration data of the on-chip Non-Volatile Memory (NVM) which is individually factory calibrated for each device. Table 4 Normal registers Addr Description R/W Bit7 Bit6 Bit5 Bit4 Bit3 Bit2 Bit1 Bit0 Default 0x00 SPI_Ctrl RW SDO_ active LSB_fi rst Softre set Softre set LSB_ first SDO_ active 0x00 0x01 Part_ID R PartID<7:0> 0x00 0x02 Status Error_code<3:0> 1’b0 DRDY 0x06 DATA_MSB R Data out<23:16> 0x00 0x07 DATA_CSB R Data out<15:8> 0x00 0x08 DATA_LSB R Data out<7:0> 0x00 0x09 TEMP_MSB R Temp out<15:8> 0x00 0x0A TEMP_LSB R Temp out<7:0> 0x00 0x30 CMD RW Sleep_time<3:0> Sco Measurement<2:0> 0x00 Reg0x00 SDO_active: 1: 4-wire SPI, 0: 3-wire SPI LSB_first: 1: LSB first for SPI interface, 0: MSB first for SPI interface Soft_reset: 1: Reset all the registers (except ‘margin’), automatically come back to 0 after reset complete. Reg0x01 PartID: OTP programmed 8 bits Part ID, corresponding to OTP register Reg0xA4. Read only from the address 0x01. Reg0x02 DRDY : 1,indicates once conversion complete, and the output data is ready for reading. WF5805F WF5805F WF5805F WF5805F WF5805F WF5805F Tel: +86-755- E-mail: 23311175 sales@weifengheng.com http://www.weifengheng.com Rev. 1.0Error_code: When diagnostic function enabled, These bits stores the error information. Error_code[3]: VINP short to VDD Error_code[2]: VINP short to GND Error_code[1]: VINN short to VDD Error_code[0]: VINN short to GND Reg0x06-Reg0x08 Data_out: 24 bits ADC output data when ‘raw_data_on’= 0 with an LSB equals to (1/64). 24 bits calibrated data when ‘raw_data_on’ = 1. Reg0x09-Reg0x0a Temp_out: Temperature output with an LSB equals to (1/256)℃. Reg0x30 Sleep_time<3:0>: 0000:0ms, 0001:62.5ms, 0010:125ms ... 1111: 1s, only active during sleep mode conversion. Measurement_control<1:0>: 000b, indicate a single shot temperature signal conversion. 001b, indicate a single shot sensor signal conversion. 010b: indicate a combined conversion (once temperature conversion immediately followed by once sensor signal conversion). 011b: indicate a sleep mode conversion (periodically perform once combined conversion with an interval time of ‘sleep_time’), 100b: OTP programming mode, enter this mode to when programming OTP banks. Sco: 1, Start of conversion, automatically come back to 0 after conversion ends (except sleep mode conversion). 4.2 OTP Registers Table 5 OTP registers Addr Description R/W Bit7 Bit6 Bit5 Bit4 Bit3 Bit2 Bit1 Bit0 Default 0xA4 PartID RW PartID<7:0> OTP 0xA5 Sys_config RW P_T_ration<1:0> Regul ator_ sel Unipo lar Raw _dat a_on DIAG _on OTP 0xA6 P_config RW 1’b01 Gain_P<2:0> OSR_P<2:0> OTP 0xA7 T_config_1 RW 1’b11 Gain_T<2:0> OSR_T<2:0> OTP WF5805F Tel: +86-755- E-mail: 23311175 sales@weifengheng.com http://www.weifengheng.com Rev. 1.0 Reg0xA4 PartID: OTP programmed 8 bits Part ID, also can be read from address 0x01. Reg0xA5 P_T_ratio: set how many sensor signal conversions performed after once temperature conversion during analog output mode. 00: 64 times, 01: 32 times, 10: 16 times, 11: once. Regulator_sel: 0: set the VEXT voltage to be 1.8V, 1: set the VEXT voltage to be 3.6V. Unipolar: 0: ADC output in bipolar format, 1: ADC output in unipolar format. (Only take effect when ‘raw_data_on’ = 1) Raw_data_on: 0: output calibrated data, 1: output ADC raw data. (Only take effect in single shot sensor signal conversion and single shot temperature conversion) Diag_on: 1, Enable diagnosis function. Reg0xA6 Input Swap: Swap VINP and VINN inside the Gain_P: set the gain of the sensor signal conversion channel. 000: gain=1, 001: gain=2, 010: gain=4, 011: gain=8, 100: gain=16, 101: gain=32, 110: gain=64, 111: gain=128. OSR_P: set the over sampling ratio of the sensor signal conversion channel. 000:1024X, 001:2048X, 010:4096X, 011:8192X, 100:256X, 101:512X, 110:16384X, 111:32768X. Reg0xA7 Gain_T: set the gain of the temperature conversion channel. 000: gain=1, 001: gain=2, 010: gain=4, 011: gain=8, 100: gain=16, 101: gain=32, 110: gain=64, 111: gain=128. OSR_T: set the over sampling ratio of the temperature conversion channel. 000:1024X, 001:2048X, 010:4096X, 011:8192X, 100:256X, 101:512X, 110:16384X, 111:32768X. WF5805F. WF5805F Tel: +86-755- E-mail: 23311175 sales@weifengheng.com http://www.weifengheng.com Rev. 1.0 5 SPI interface provides both SPI and I2C interface for serial communication and ‘CSB’ pin is used to switch between these two protocols. Pulling ‘CSB’ pin low selects the SPI interface, leaving ‘CSB’ pin float or puling it high selects the I2C interface. 5.1 Interface Specification Table 6 SPI interface specification Symbol Parameter Condition Min Max Unit fsclk Clock frequency Max load on SDIO or SDO=25pF 10 MHz tsclk_l SCLK low pulse 20 ns tsclk_h SCLK high pulse 20 Tsdi_setup SDI setup time 20 ns Tsdi_hold SDI hold time 20 ns Tsdo_od SDO/SDI output delay Load = 25pF 30 ns Load = 250pF 40 Tcsb_setup CSB setup time 20 ns Tcsb_hold CSB hold time 40 ns The figure below shows the definition of the SPI timing given in table 6 Figure 4 SPI timing diagram The falling edge of CSB, in conjunction with the rising edge of SCLK, determines the start of framing. Once the WF5805F WF5805F Tel: +86-755- E-mail: 23311175 sales@weifengheng.com http://www.weifengheng.com Rev. 1.0 beginning of the frame has been determined, timing is straightforward. The first phase of the transfer is the instruction phase, which consists of 16 bits followed by data that can be of variable lengths in multiples of 8 bits. If the device is configured with CSB tied low, framing begins with the first rising edge of SCLK. The instruction phase is the first 16 bits transmitted. As shown in Figure 5.2, the instruction phase is divided into a number of bit fields. Figure 5 Instruction Phase Bit Filed The first bit in the stream is the read/write indicator bit (R/W). When this bit is high, a read is being requested, otherwise indicates it is a write operation. W1 and W0 represent the number of data bytes to transfer for either read or write (Table 5.2). If the number of bytes to transfer is three or less (00, 01, or 10), CSB can stall high on byte boundaries. Stalling on a nonbyte boundary terminates the communications cycle. If these bits are 11, data can be transferred until CSB transitions high. CSB is not allowed to stall during the streaming process. The remaining 13 bits represent the starting address of the data sent. If more than one word is being sent, sequential addressing is used, starting with the one specified, and it either increments (LSB first) or decrements (MSB first) based on the mode setting. Table 7 W1 and W0 settings W1:W0 Action CSB stalling 00 1 byte of data can be transferred. Optional 01 2 bytes of data can be transferred. Optional 10 3 bytes of data can be transferred. Optional 11 4 or more bytes of data can be transferred. CSB must be held low for entire sequence; otherwise, the cycle is terminated. No Data follows the instruction phase. The amount of data sent is determined by the word length (Bit W0 and Bit W1). This can be one or more bytes of data. All data is composed of 8-bit words. Data can be sent in either MSB-first mode or LSB-first mode (by setting ‘LSB_first’ bit). On power up, MSB-first mode is the default. This can be changed by programming the configuration register. In MSB-first mode, the serial exchange starts with the highest-order bit and ends with the LSB. In LSB-first mode, the order is reversed. (Figure 5.3) WF5805F Tel: +86-755- E-mail: 23311175 sales@weifengheng.com http://www.weifengheng.com Rev. 1.0 Figure 6 MSB First and LSB First Instruction and Data Phases Register bit ‘SDO_active’ is responsible for activating SDO on devices. If this bit is cleared, then SDO is inactive and read data is routed to the SDIO pin. If this bit is set, read data is placed on the SDO pin. The default for this bit is low, making SDO inactive. WF5805F Tel: +86-755- E-mail: 23311175 sales@weifengheng.com http://www.weifengheng.com Rev. 1.0 6 I2C INTERFACE I2C bus uses SCL and SDA as signal lines. Both lines are connected to VDDIO externally via pull-up resistors so that they are pulled high when the bus is free. The I2C device address of is shown below. The LSB bit of the 7bits device address is configured via SDO/ADDR pin. Table 8 I2C Address A7 A6 A5 A4 A3 A2 A1 W/R 1 1 0 1 1 0 SDO/ADDR 0/1 Electrical specification of the I2C interface pins Symbol Parameter Condition Min Max Unit fscl Clock frequency 400 kHz tLOW SCL low pulse 1.3 us tHIGH SCL high pulse 0.6 us tSUDAT SDA setup time 0.1 us tHDDAT SDA hold time 0.0 us tSUSTA Setup Time for a repeated start condition 0.6 us tHDSTA Hold time for a start condition 0.6 Us tSUSTO Setup Time for a stop condition 0.6 Us tBUF Time before a new transmission can start 1.3 Us Figure 7 I2C Timing Diagram The I2C interface protocol has special bus signal conditions. Start (S), stop (P) and binary data conditions are shown below. At start condition, SCL is high and SDA has a falling edge. Then the slave address is sent. After the 7 address bits, the direction control bit R/W selects the read or WF5805F WF5805F Tel: +86-755- E-mail: 23311175 sales@weifengheng.com http://www.weifengheng.com Rev. 1.0 write operation. When a slave device recognizes that it is being addressed, it should acknowledge by pulling SDA low in the ninth SCL (ACK) cycle. At stop condition, SCL is also high, but SDA has a rising edge. Data must be held stable at SDA when SCL is high. Data can change value at SDA only when SCL is low. Figure 8 I2C Protocol WF5805F Tel: +86-755- E-mail: 23311175 sales@weifengheng.com http://www.weifengheng.com Rev. 1.0 WF5805F Tel: +86-755- E-mail: 23311175 sales@weifengheng.com http://www.weifengheng.com Notes: ? The recommended value for C1 is 100nF ? The value for the pull-up resistors R1, R2 should be based on the interface timing and the bus load; a normal value of R1 is 4.7kΩ, R2 is 4.7kΩ. R1 R2 C1 7 Connection diagram WF5805F Rev. 1.0 Tel: +86-755- E-mail: 23311175 sales@weifengheng.com http://www.weifengheng.com 8 Package, reel and environment Notes: Mechanical dimension is mm 8.1 Information Package 8.2 Pin Configuration 8.3 ipping Package Sh Rev. 1.0 Tel: +86-755- E-mail: 23311175 sales@weifengheng.com http://www.weifengheng.com WF5805F Rev. 1.0 9 Soldering recommendation The recommended soldering profile is shown in Figure 12, followed by a description of the profile features in Table 10. Figure 12 Recommended Soldering Profile Table 10 Recommended Soldering Profile Profile Feature Pb-Free Average ramp-up rate(TsMax to TP) 3℃/sec max. Preheat: -Temperature Min.(TsMin) -Temperature Max.(TxMax) -Time.(TsMin to TsMax)(Ts) 150℃ 200℃ 60 sec to 180 sec Time maintained above: -Temperature(TL) -Time(tL) 217℃ 60 sec to 150 sec Peak temperature(TP) 260℃ Time within 5℃ of actual peak temperature(TP)2 20 sec to 40 sec Ramp-down rate 4℃/sec max. Time 25℃ to peak temperature 8 minutes max. WF5805F Tel: +86-755- E-mail: 23311175 sales@weifengheng.com http://www.weifengheng.com
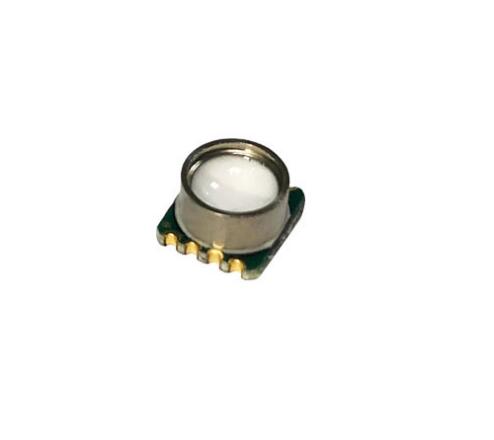