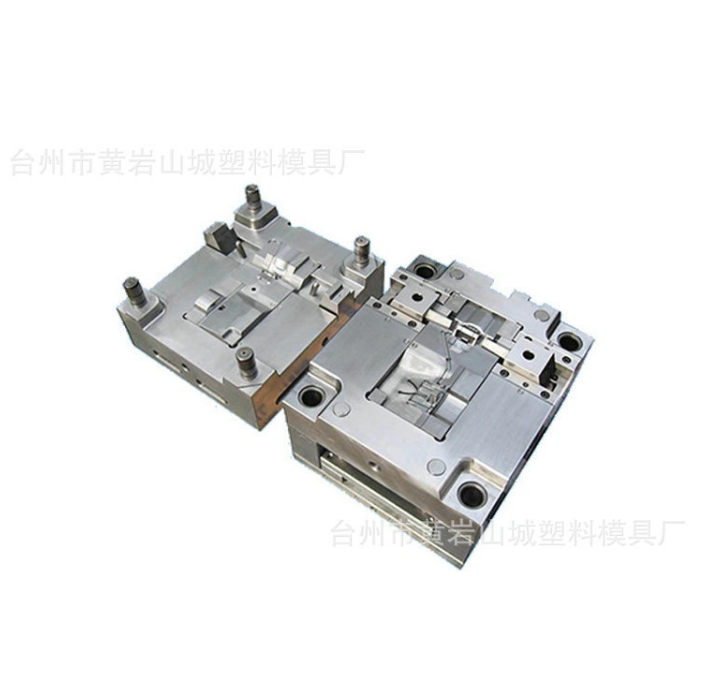
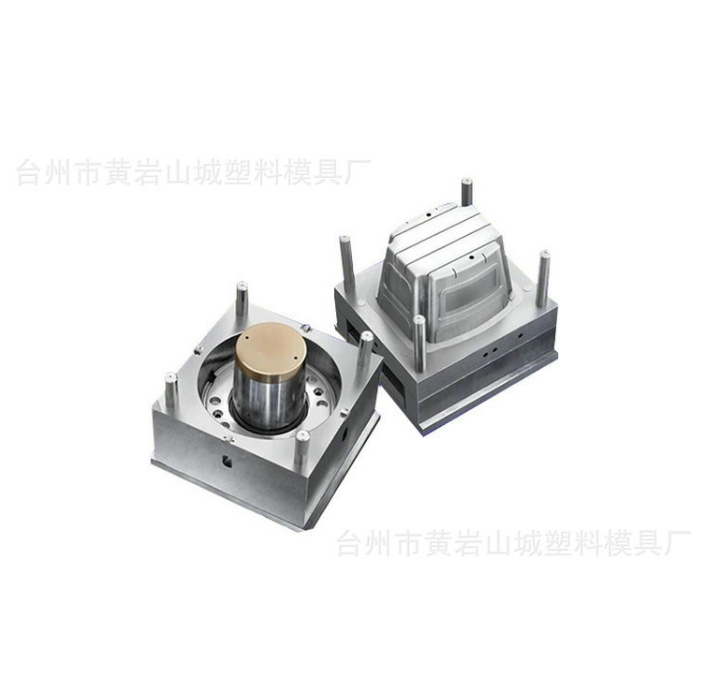
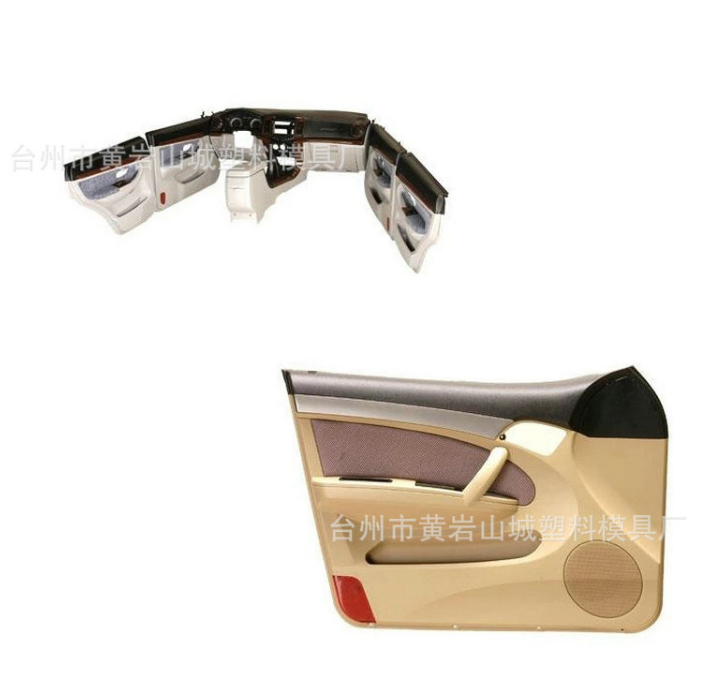
浙江省台州市黄岩山城塑料模具厂是一家集生产加工、经销批发的个体经营,注塑模具、吹塑模具、管件模具、塑料产品加工是浙江省台州市黄岩山城塑料模具厂的主营产品。浙江省台州市黄岩山城塑料模具厂是一家经国家相关部门批准注册的企业。浙江省台州市黄岩山城塑料模具厂以雄厚的实力、合理的价格、优良的服务与多家企业建立了长期的合作关系,现有员工80名 , 工程师有20名,浙江省台州市黄岩山城塑料模具厂热诚欢迎各界前来参观、考察、洽谈业务。
一.工艺分析
图(a)垫片产品图
t=2mm 材料:10钢 生产纲领:20万件/年
该制件形状一般,尺寸较小,厚度很薄,属于普通冲压件,在设计此模具时主要考虑模具材料和结构的选择,确定一定的模具寿命。但有几点要注意:
(1) 制件冲孔处要合理安排工序。
(2) 制件先冲孔后落料
(3) 应重视模具材料和结构的选择,保证一定的模具寿命。
(4) 模具结构形式的确定:因该制件较薄,为保证制件平整,采用弹压卸料装置。它还可以对冲孔小凸模起导向作用和保护作用,定位形式采用导正销形式进行精定位。工艺方案的确定:根据制件工艺性能分析,其基本工序有冲孔和落料两种。经综合分析决定采用级进模形式进行冲压。
1. 工艺方案的确定:
2. 根据制件的工艺性分析,其基本工序有冲孔,落料两种。
经分析决定采用级进模形式进行冲压。
3. 模具结构形式的确定
因为制件较薄,为了保证制件的平整,采用弹性卸料装置。它还可以对冲孔小凸模起导向作用和保护作用,定位形式采用导正销的形式进行精定位。
二.工艺设计
(1)画排样图按照该制件的材料,壁厚,以及所需冲压工艺等情况分析,则该制件需4个工步完成.条料宽度经分析计算B=95mm
图(b) 排样图
(2)、计算冲压力,完成本制件所需的冲压力由冲裁力及卸料力组成。完成本制件所需的冲压力由冲裁力,卸料力,推件力组成
冲裁力F冲—由冲孔力,切断力两部分组成.
F=KLtτb(F—冲裁力、L---冲裁周边长度、t—材料厚度、τb---材料抗剪强度(查表4—12)、K---系数)
L1冲孔周长=50*3.14=157mm
由F1冲=Ltδb
=157x2x310
=97340N
F1卸=K卸. F冲=0.05X97340N
=4867N
F1推=K推.n.F冲=0.05X3X97340N
=14601N
总冲压力:
F总=F冲+F卸+F推
=97340+4867+14601
=219015N
(3)、 初选压力机,查表4-33可知该压力机的模柄孔尺寸为直径=50,长度=70。
(4)、计算凸凹模刃口尺寸:
经过分析决定采用分开加工法计算刃口尺寸。查表得Z/min=0.13;Z/min=0.18;C/min=0.065
图(c)、 刃口尺寸计算示样图
冲孔部分计算如下:d150=(50+0.3)=50.3mm
落料部分计算如下:d290=(90+0.3)=90.3mm
(5)、卸料板各孔口尺寸:本模具卸料板的各孔是按照凸模尺寸,使其保持0.4miu间隙割出,据此原则确定尺寸。
(6) 、凸模固定板各孔口尺寸, 凸模固定板各孔与凸模配合,本模具所采用的固定形式为“挂耳”形式固定,其配合选用H7/h6配合。
(7) 确定压力中心
因为此制件为对称圆形故其压力中心为压力机的正中点.即通过模柄的中心线。
(8)凹模各孔口位置尺寸 本制件尺寸很多,其基本尺寸可以按排样图确定,经绘图检验并不存在明显不合理的分布情况。
(9)卸料板各孔尺寸 本模具卸料板的各孔是按照凸模尺寸,使保持0.4min间隙割出,根据原则确定具体的尺寸。
(10)凸模固定板的尺寸 凸模固定板各孔与凸模配合,本模具所采用的固定形式觉为“挂耳”形式固定,其配合选用H7/h6配合。
(11)计算冲孔凸模,凹模刃口尺寸:由于本制件形状比较规则,根据情况分别采用分开加工法和配合法计算刃口尺寸。
三.模具结构设计:
(1)凹模设计:因制件形状较复杂,根据只有两个公步,根据具体情况决定选用整体式矩形凹模。为了保证模具寿命,选用9Mn2V为凹模材料
(2)选择模架及确定其它冲模零件尺寸:由于制件本身特点决定标准模架,其它冲模零件也按照以标准形式为参考或直接选用标准件等原则进行选用。
A. 确定凹模厚度H值.
B. 确定凹模周界尺寸LXB:426X170
(2)选择模架及确定其它冲模零件尺寸.
由制件本身的特点决定选用标准模架。
(3)根据此标准可画出模架图和其它零件尺寸参数。
上模座: 426χ326χ35
下模座: 426χ326χ50
模柄 : A50X105
卸料螺钉 :M10X12X72
初挡料板:20χ77.5χ1.8
定位销 :8jX70
导柱: 28h5X170
导套: 28H6X85X33
弹簧: YA1.6X16X40
凸模长度:83,81(75),79(73),77(71)
凸模固定板:(1)Φ100.8χ5, Φ89.8χ25(2) Φ60.8χ5, Φ49.8χ25(3)Φ38.8χ5, Φ27.8χ25(4)Φ25χ5, Φ14.2χ25
卸料板:(1)Φ90.8χ15, (2) Φ50.8χ15(3)Φ28.8χ15 (4)Φ15χ15
(5) 脱料加于说明:根据导正的结构形式应用(冷冲压工艺及模具设计教程)p47。用于d=10mm~25mm的孔。D(H7/s6)取板料厚度的0.8~1.2倍。直径略小于制件冲孔直径。材料用T10A,Cr12或9Mn2v热处理硬度为52HRc~56HRc。仅对条料起粗略定位作用。
(6)由图可知制件需按配合法计算,计算时都是先加工好凸模作为基准件,然后根据此基准件的实际尺寸,配做凹模。使它们保持一定间隙,由于形状工件各部分尺寸性质不同,凸模和凹模磨损后,尺寸变化的趋势不同,所基准件的刃口尺寸计算的方法也不同。
四、按尺寸画出装配图和零件图:
根据以上的分析,计算等具体结果,先绘装配图,再根据装配图折画零件图,并标注尺寸,书写加工说明书。
图(d)开模状态主视装配图
1、 下模板;2、凹模;3、螺钉;4、卸料板;5、导套;6、上模板;7、卸料螺钉;
8、垫板;9、凸模;10、凸模;11、凸模;12、凸模;13、模柄;14、定位销;15、螺钉;16、凸模固定板;17、弹簧;18、导料板;19、导柱;20、定位销;21、螺钉;22、初挡料板;23、弹簧;
五 、装配
1. 准备所有工具和量具(如内六角螺钉)
2. 装备、先装拉深模工作零件(如凹模、凸模)装下模部分
3. 然后装垫板、固定板、料板等零部件。
4. 上、下模装上销钉,并拧紧螺钉。
5. 总装其它零件。
。
六 、结束语
一套好的模具新要在结构上简便合理,制造容易使用方便、寿命长、成本低的情况下能加工出合格的产品
7.模具零件制造工艺卡
表1凹模板机械加工工艺过程卡
凹模板机械加工工艺过程卡 模具名称:垫圈连续模 零件名称:凹模
材料 名称 毛坯种类 毛坯尺寸 零件质量 件数 更改内容
牌号 9Mn2V 板料 430*174*34 1
序号 工序内容 加工车间 设备名称编号 工艺装备 工时定额
1 下料:430*174*34 备料车间 锯床
2 铣:铣平面、426.1*171*31 模具车间 立铣 虎钳
3 磨:磨平面、426.1*171*31 模具车间 磨床
4 划线:划中心、螺纹孔、固定销 模具车间
5 钻:中心钻线孔、各螺钉、销钉线孔、攻牙M10 模具车间 立钻 平行夹头
6 热处理:硬度为HRC60~64, 热处理车间 加热炉
7 线割:割R4固定削、R45 R25 R14R7.1孔有斜度为1度。 模具车间 线割机
8 磨:精磨下平面至尺寸要求 模具车间 平面磨
9 检验:按图样检验
技术要求:各安装、定位孔加工后,进行淬火处理,硬度为HRC60~64,采用线切割加工凹模孔,并达到尺寸要求。
表2凸模固定板机械加工工艺过程卡
凸模固定板机械加工工艺过程卡 模具名称:垫圈连续模 零件名称:凸模固定板 共 1 页 第1 页
材料 名称 毛坯种类 毛坯尺寸 零件质量 件数 更改内容
牌号 45 板料 430*174*34 1
序号 工序内容 加工车间 设备名称编号 工艺装备 工时定额
1 下料:430*174*34 备料车间 锯床
2 铣:铣平面、426.1*171*31 模具车间 立铣 虎钳
3 磨:磨平面、426*170*30 模具车间 磨床
4 划线:划中心、螺纹孔、固定销 模具车间
5 钻:中心钻线孔、各螺钉、销钉线孔、攻牙M10 模具车间 立钻 平行夹头
6 热处理:HRC53~55 热处理车间 加热炉
7 线割:割R4固定削、R45 R25 R14R7.1孔有斜度。 模具车间 线割机
8 磨:精磨下平面至尺寸要求 模具车间 平面磨
9 检验:按图样检验
编制 校对 审核 会签
技术要求:采用线切割加工两个大的凸模安装孔,其余各孔采用钻和铣削加工,并达到尺寸要求,销孔进行铰削,表面精度为1.6μm。
表3卸料板机械加工工艺过程卡
卸料板机械加工工艺过程卡 模具名称:垫圈连续模 零件名称:卸料板 共 1 页 第1 页
材料 名称 毛坯种类 毛坯尺寸 零件质量 件数 更改内容
牌号 45 板料 430*174*19 1
序号 工序内容 加工车间 设备名称编号 工艺装备 工时定额
1 下料:430*174*19 备料车间 锯床
2 铣:铣平面、426.1*171*16 模具车间 立铣 虎钳
3 磨:磨平面、426*170*30 模具车间 磨床
4 划线:划中心、螺纹孔、固定销 模具车间
5 钻:中心钻线孔、各螺钉、销钉线孔、攻牙M10 模具车间 立钻 平行夹头
6 热处理:HRC53~55 热处理车间 加热炉
7 线割:割R4固定削、R45 R25 R14R7.1孔有斜度。 模具车间 线割机
8 磨:精磨下平面至尺寸要求 模具车间 平面磨
表5垫板机械加工工艺过程卡
垫板机械加工工艺过程卡 模具名称:垫圈连续模 零件名称:垫板 共 1 页 第1 页
材料 名称 毛坯种类 毛坯尺寸 零件质量 件数 更改内容
牌号 45 板料 430*174*10 1
序号 工序内容 加工车间 设备名称编号 工艺装备 工时定额
1 下料:430*174*10 备料车间 锯床
2 铣:铣平面、426.1*171*7 模具车间 立铣 虎钳
3 磨:磨平面、426*170*6 模具车间 磨床
4 划线:划中心、螺纹孔、固定销 模具车间
5 钻:中心钻线孔、各螺钉、销钉线孔、攻牙M10 模具车间 立钻 平行夹头
6 热处理:硬度为HRC43~48 热处理车间 加热炉
7 线割:割R4固定削、R6.5 R5.5 R14 模具车间 线割机
8 磨:精磨下平面至尺寸要求 模具车间 平面磨
9 检验:按图样检验
技术要求:过孔加工完后,进行淬火处理,硬度为HRC43~48,销孔采用线切割加工。
表6导料板机械加工工艺过程卡
导料板机械加工工艺过程卡 模具名称:垫圈连续模 零件名称:导料板 共 1 页 第1 页
材料 名称 毛坯种类 毛坯尺寸 零件质量 件数 更改内容
牌号 45 板料 430*41*9 1套
序号 工序内容 加工车间 设备名称编号 工艺装备 工时定额
1 下料:430*41*9 备料车间 锯床
2 铣:铣平面、427*38*6 模具车间 立铣 虎钳
3 磨:磨平面、426*37*5 模具车间 磨床
4 划线:划中心、螺纹孔、固定销 模具车间
5 钻:中心钻线孔、 模具车间 立钻 平行夹头
6 热处理:硬度为HRC43~48 热处理车间 加热炉
7 线割:割R4固定削、 模具车间 线割机
8 磨:精磨下平面至尺寸要求 模具车间 平面磨
9 检验:按图样检验
表7上模座板机械加工工艺过程卡
上模座板机械加工工艺过程卡 模具名称:垫圈连续模 零件名称:上模座板 共 1 页 第1 页
材料 名称 毛坯种类 毛坯尺寸 零件质量 件数 更改内容
牌号 HT200 板料 430*330*39 1
序号 工序内容 加工车间 设备名称编号 工艺装备 工时定额
1 下料:430*330*39 备料车间 锯床
2 铣:铣平面、426.1*327*36 模具车间 立铣 虎钳
3 磨:磨平面、426*326*35 模具车间 磨床
4 划线:划中心、螺纹孔、固定销 模具车间
5 钻:中心钻线孔、各螺钉、销钉线孔、攻牙M10 模具车间 立钻
6 沉孔:R30.5*8,9.5*24,8*11
7 热处理:HRC53~55 热处理车间 加热炉
8 线割:割R4固定削、R21 R30.5 R25.5R9.5R6.5R8 模具车间 线割机
9 磨:精磨下平面至尺寸要求 模具车间 平面磨
10 检验:按图样检验
编制 校对 审核 会签
技术要求:模柄孔和导套孔采用钻和铣削加工,其余用钻削加工,并达到尺寸要求,销孔进行铰削,表面精度为1.6μm。导套孔与大平面的垂直度为±0.01mm。
表8下模座板机械加工工艺过程卡
下模座板机械加工工艺过程卡 模具名称:垫圈连续模 零件名称:下模座板 共 1 页 第1 页
材料 名称 毛坯种类 毛坯尺寸 零件质量 件数 更改内容
牌号 HT200 板料 430*330*54 1
序号 工序内容 加工车间 设备名称编号 工艺装备 工时定额
1 下料:430*330*54 备料车间 锯床
2 铣:铣平面、426.1*327*51 模具车间 立铣 虎钳
3 磨:磨平面、426*326*50 模具车间 磨床
4 划线:划中心、螺纹孔、固定销 模具车间
5 钻:中心钻线孔、各螺钉、销钉线孔、攻牙M10 模具车间 立钻 平行夹头
6 沉孔:R8*11 模具车间
7 热处理:HRC53~55 热处理车间 加热炉
8 线割:割R4固定削、R45.1 R25.1 R15R8.5R15.1R5.5 模具车间 线割机
9 磨:精磨下平面至尺寸要求 模具车间 平面磨
10 检验:按图样检验
编制 校对 审核 会签
技术要求:模柄孔和导套孔采用钻和铣削加工,其余用钻削加工,并达到尺寸要求,销孔进行铰削,表面精度为1.6μm。导套孔与大平面的垂直度为±0.01mm。
软水机内芯注射模毕业设计课题说明书
1. 引言
随着人民生活水平的提高,饮水机将走进千家万户,成为人民不可或缺的家用器具,因此其具有广阔的市场前景,受到不少商家们的青睐。在此仅讲叙饮水机的一个重要零件——饮水机内芯的设计。
2.产品结构分析
塑件零件图如图1-a所示,实体如图1-b所示。材料为高密度聚乙烯(HDPE),又称低压聚乙烯,为支链很少的线型分子结构,结晶度为80%-90%,相对分子质量大,耐热性高,耐化学性好,刚性好,硬度大、力学强度较高;湿性小,流动性极好,溢边值0.02mm左右,流动性对压力变化敏感;加热时间长则发生分解、烧伤;材料收缩率范围大,收缩值也大,模具设计时
图1-b产品实体图
取收缩率范围的中间值2%.从产品结构图可以看出, 其四周均布有与水平分型面平行的四个小凸台,因此,只要采用一个水平分型面A和四个小型侧分型抽芯机构就很容易实现脱模.
3.模具结构设计及其主要零件的加工说明
模具结构如图2所示。根据产量的要求,再考虑到产品尺寸较大,模具采用一模一腔并用三板模的结构形式。
模具选用了龙记标准模架,其型号为4040-DAI-A板40-B板150-C板150。由于产量的要求,模具成型零件部分必须采用特殊钢材,在此选用从瑞典进口的钢材8407,因此,模具的A板和B板的中心部分必须铣空用于镶成型零件,由于成型零件的模芯部分较大,为了加工的方便和节省加工费用把它设计成为通孔的形式,这样把A板和B板叠在一起加工出来模芯部分的对中性较好。把型芯镶块用螺钉固定在托板3上,同时托板3又起支撑的作用,为了模具的安全起见增加了四个支撑柱29,以承受塑料熔体在成型过程中较大的注射压力,防止型腔部分变形而影响塑件质量。
另外,塑件有一个¢136mm、深0.5mm凹陷(如图1-a)所示,为了节省材料和利用这个小凹陷在型芯镶块18中又镶了一块定模型芯
25,为了使型腔镶块26的加工方便也在上另增加了一个动模型芯27。加工时,型芯镶块18采用铣削加工;定模型芯25外圆采用车削加工,其内凹部分由于有小凸起,采用电火花成型加工;型腔镶块26的型腔部分也采用车削加工,而成型塑件的加强筋部分由于宽度过窄则用电火花加工。
4.模具的工作过程
模具的工作过程为:将制作好了的模具装配到卧式注射机上,注射成形后开模时,在弹簧19的作用下模具首先在A板6与水口推板7之间开模,此时点浇口被拉断,浇注系统凝料留于定模一侧(如图4a所示)。动模移动一段距离以后,A板6与限位拉杆24左端接触时,动、定模分型(即A板与B板之间分型),动模继续移动一段距离,在推出机构的作用下把塑件推出,此时塑件自动落下(如图4b所示),在拉板28的作用下,通过A板6和拉杆24使水口推板7与水口板8之间分型,分开距离由限位螺钉17控制。此时,浇注系统凝料脱离
5.B板 6.A板 7.水口推板 8.水口板 9.分浇道拉料杆 16弹顶装置 17.限位螺钉 19.弹簧 24.限位拉杆 28.拉板 31.33.顶针 39.楔紧块 42.斜导柱 47.水口边钉 48.注射机顶杆
图3.模具的开启状态
分浇道拉料杆9,并在弹顶装置16的作用下,弹至A板与水口推板之间而自动落下(如图4c所示)。
图4.模具的开启过程
5.注射成型工艺所要注意的问题
注射成型时,螺杆转速30~60r/min,喷嘴温度150~180℃,料筒温度前段180~190℃、中段180~200℃、后段140~160℃,模具温度控制在30~60之间,注射压力70~100Mpa。模具调试时应经过多次试调直到得到成形出塑件参数为止。
6.结束语
采用点浇口时,模具为三板式,其浇注系统凝料一般由人工取出。为了提高生产率,缩短成型周期,省去从塑件人工去除浇口的工序,该模具在设计时采用了点浇口的自动切断机构,适用于全自动化生产