厂商 :东莞市正信激光科技有限公司业务部
广东 东莞- 主营产品:
- 不锈钢激光焊接机
- 模具激光焊接机
- 水龙头激光焊接机
联系电话 :13650457101
商品详细描述
电池外壳激光焊接机超级电容铝壳自动焊接设备
新能源汽车的电池可靠性、成本高、产能缺乏等问题是一个世界型的难题,现有电池技术的可靠性、稳定性不足,产品的循环寿命不长等因素长期以来一直影响着新能源汽车的发展。近年来,各主要汽车厂商在新能源汽车方面投入了巨大的研发费用,也取得了很大的进展。可以预见,未来十年,将是新能源汽车爆发式增长的十年。
深圳市正信激光科技有限公司密切配合各电池生产厂家,共同研发汽车动力电池的激光焊接技术,取得了很大的进展。到目前为止,已经为国内上百家动力电池生产厂家设计制作了全自动或半自动的激光焊接生产线,取得了非常丰富的实践经验。
一、动力电池激光焊接的主要部位
动力电池的电芯按其外型可分三种,分别是方型、圆柱型以及软包电芯(见图1)。壳体的材料主要有铝材和不锈钢,但以铝材为主,其中以1000系和3000系较多。
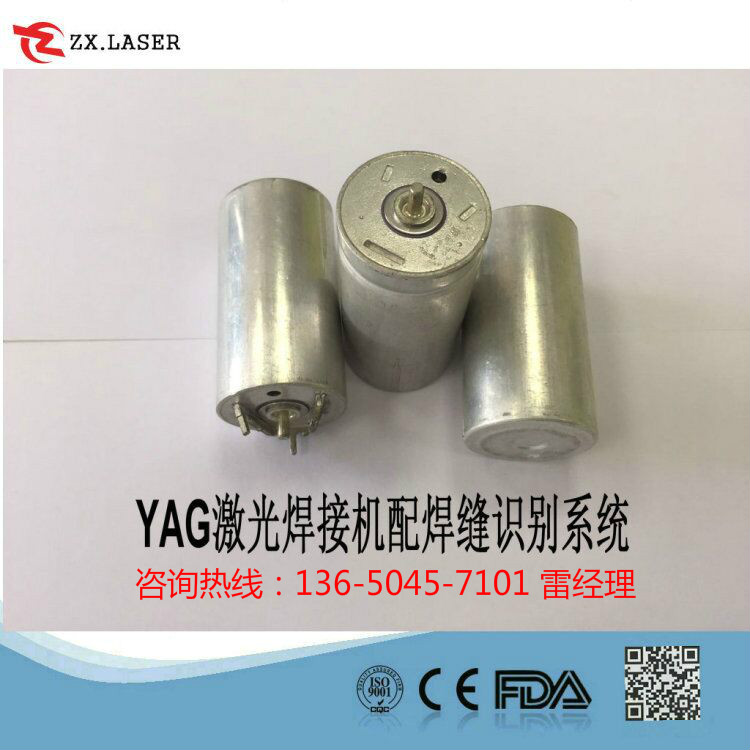
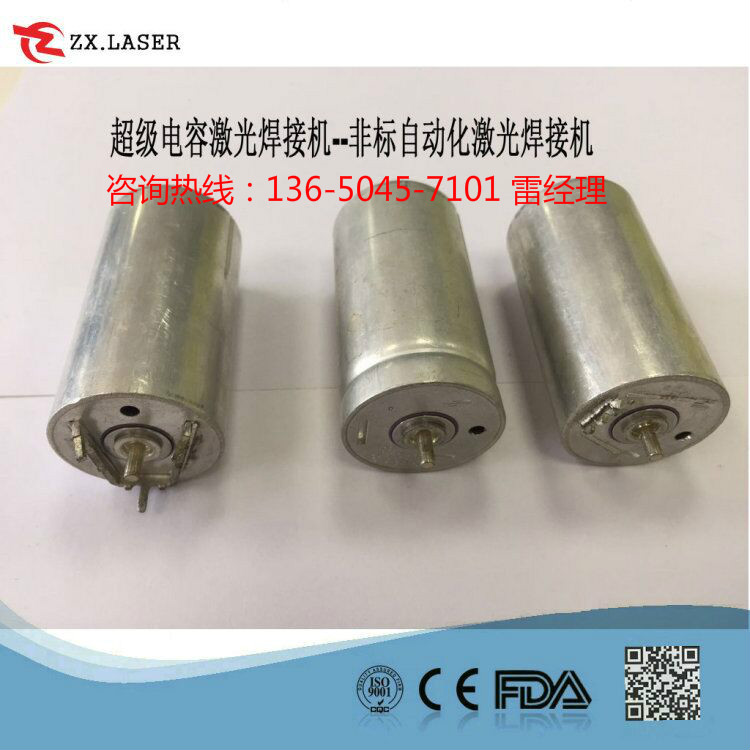
图1 常见动力电池外形
目前,在国内生产的电动汽车当中,这三种电池都有应用:例如比亚迪E6和K9电动车使用的是方型电池;杭州万向为电芯供应商的一些电动车厂家使用其软包电池;上汽系某些电动车车型则使用美国A123公司的圆型电池。这三种电池的自动化激光焊接系统及工艺也各不相同;整体而言,以方形电池居多。
各种电池的激光焊接部位主要有四种:壳体的封装,根据位置的不同分为顶盖、底盖和侧面的焊接、顶盖防爆片及安全盖的焊接、密封钉(也叫注液口)的焊接、电芯极耳与顶盖的焊接。另外,超级电容的焊接以连接片和负极封口焊接为主。各种动力电池及超级电容的焊接部位如图2所示。
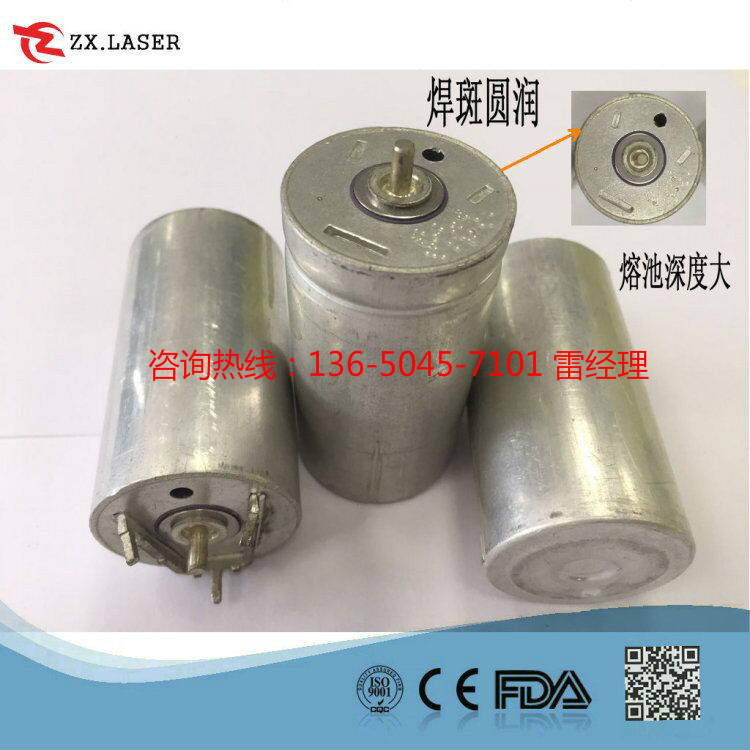
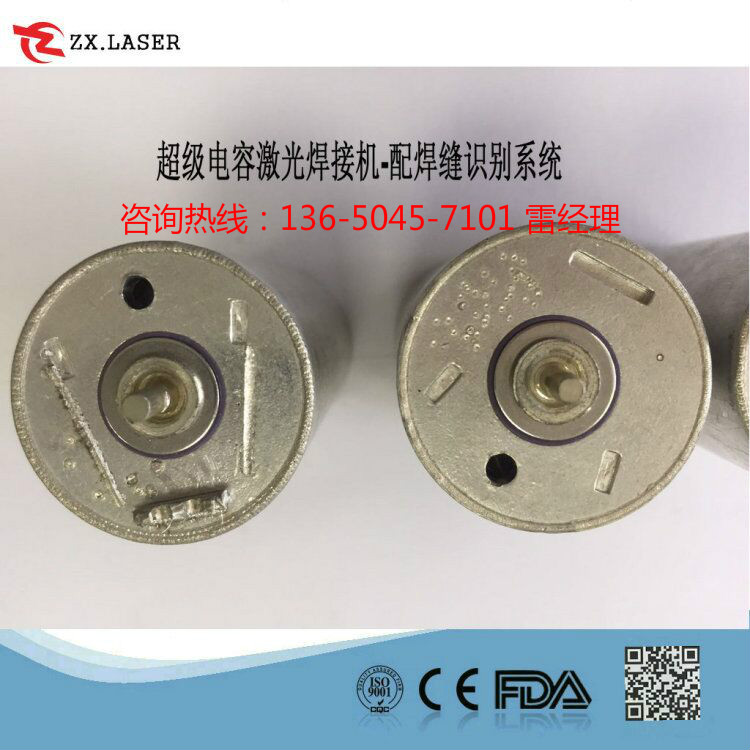
图2 各种电池的激光焊接焊接部位
二、动力电池焊接的工艺难点
一般壳体厚度都要求达到1.0毫米以下,主流厂家目前根据电池容量不同壳体材料厚度以0.6mm和0.8mm两种为主。焊接方式主要分为侧焊和顶焊,其中侧焊的主要好处是对电芯内部的影响较小,飞溅物不会轻易进入壳盖内侧。由于焊接后可能会导致凸起,这对后续工艺的装配会有些微影响,因此侧焊工艺对激光器的稳定性、材料的洁净度和顶盖与壳体的配合间隙有较高的要求。而顶焊工艺由于焊接在一个面上,可采用更高效的振镜扫描焊接方式,但对前道工序入壳及定位要求很高,对设备的自动化要求高。
目前铝壳电池占整个动力电池的90%以上。铝材的激光焊接难度较大,会面临焊痕表面凸起问题、气孔问题、炸火问题、内部气泡问题等。表面凸起、气孔、内部气泡是激光焊接的致命伤,很多应用由于这些原因不得不停止或者想办法规避。很多电池厂家在研发初期都会为此大伤脑筋,究其原因,主要是采用的光纤芯径过小或者激光能量设置过高所致。引起炸火(也称飞溅,Splash)的因素也很多,如材料的清洁度、材料本身的纯度、材料自身的特性等,而起决定性作用的则是激光器的稳定性。在动力电池焊接当中,焊接工艺技术人员会根据客户的电池材料、形状、厚度、拉力要求等选择合适的激光器和焊接工艺参数,包括焊接速度、波形、峰值、焊头倾斜角度等来设置合理的焊接工艺参数,以保证最终的焊接效果满足动力电池厂家的要求。
方形电池由于来料的配合精度等方面的因素影响,焊接时拐角处最容易出现问题,需要在根据实际情况不断探索,调整焊接速度可以解决这类问题。圆形电池没有这方面的问题,但后续集成成电池模组的难度较大。
三、动力电池的激光自动化焊接系统简介
图3是一条方形动力电池全自动激光焊接线,含两条由焊接、泄漏检测、短路检测及编码打标为主要功能的产线,产能≧16PPM,焊接强度6kgf/c㎡以上不泄漏。
本系统可依次完成电池的激光焊接,气密性测试,短路测试,电池打标,不合格品自动剔除等相关工序。
激光焊接部份由激光器,激光焊接头,XYZ三轴运动控制轴,旋转机构,电池夹具(压紧及较正夹具),上下料机械手等构成,其主要作用是:将电池从流水线上夹持到焊接工作台进行焊接作业,并焊接完成后放回流水线上。
气密性及短路测试部份由气密性测试组件,短路测试组件,内部流水线输送系统,检测上料机械手,检测下料机械手等构成,其主要作用是:将流水线上焊接完成后的电池夹持到内部流水线输送系统上,依次对其进行定位,气密性,短路相关测试,并在检测完成后将良品抓回回到主流水线上,不良品抓除到废料盒中。测漏部分采极与盖板三方测试功能。
打标部份由激光打标机,抓取定位机构等构成,其主要作用是对焊接后产品进行打标。可在金属产品(含铝材)一用正压检测,短路测试具有正负极之间、正极与盖板、负侧正上部分高速的标记出12位数字加字母码(其中三位字母码,9位数字码),加8*8的二维码。
流水线部份由流水线倍速链,夹具托盘,定位气缸,挡隔分料气缸等构成,其主要作用是带动电池到相应的位置,方便焊接与检测,并具有一定的储料功能。
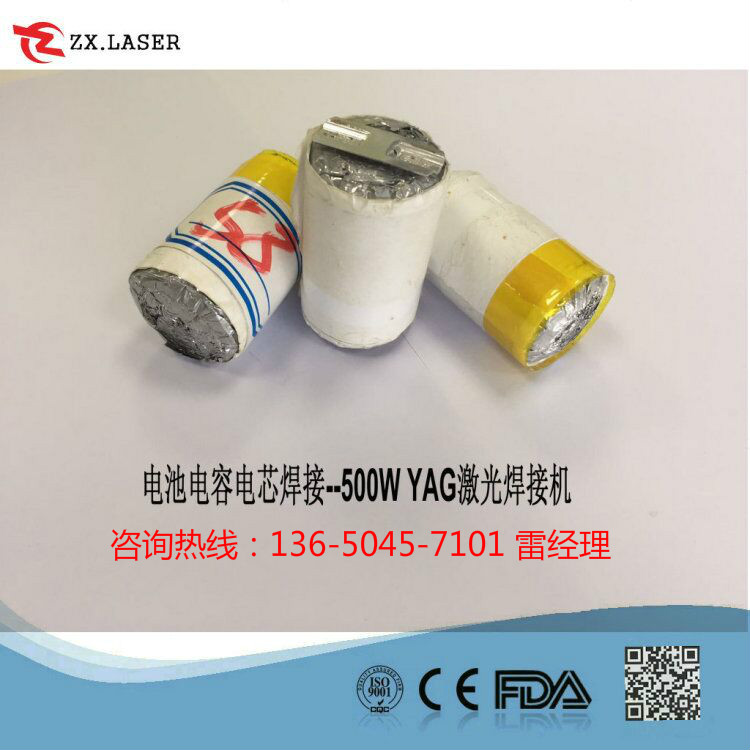
图3 方形动力电池全自动激光焊接线
图4是一种方形电池顶盖的半自动生产线,焊接工作台部分采用工业PLC控制,可焊接电池范围为H:130-300mm、W:110-250mm、T:20--50mm,焊接图形轨迹为平面矩形,焊接过程自动化。
该系统可配合环形输送线用于电池顶盖与壳体自动激光密封焊接,其中顶盖和壳体材料为不锈钢或铝合金。焊接参数可以通过操作界面进行设定,焊接完后确保焊缝无渗漏,焊接完后符合耐压测试要求,不会对电池周围部件形成破坏或者损伤,且具备自动和手动两种功能。
图4 方形动力电池顶盖自动激光焊接线
四、总结
通过高效精密的激光焊接可以大大提高汽车动力电池的安全性、可靠性和使用寿命,必将为今后的汽车动力技术带来革命化进步。动力电池的激光焊接部位多,有耐压和漏液测试要求,材料多数为铝材,因此焊接难度大,对焊接工艺的要求更高。今后,大多数厂家需要全自动生产线,将进一步增加焊接系统的集成难度。高质量的动力电池需要生产厂家的设计人员和激光焊接技术人员密切协作,从材质、形状、厚度、工艺、实时检测等各方面优化设计,才能达到理想的焊接效果。
相关产品推荐