厂商 :广州莱宁换热设备有限公司
广东 广州- 主营产品:
- 板式换热器
- 换热机组
- 钎焊板式换热器
联系电话 :13922376553
商品详细描述
板式换热器供应厂家浙江换热器
广州莱宁
2)管束变形
在换热器管束检修清洗过程中,看到有许多管子弯曲变形,尤以外围管束最为严重,变形管束约占2/5,但管子均畅通。检查中还发现折流挡板不同程度变形。
如前所述,原料中的焦粉及其它杂质过多,线速较低易形成结焦,结焦形成的不流动区导致该区域管束内外温度趋近相同,即接近油浆的温度365℃。而流动 区壳程原料油的温度一般由70℃升至200℃,于是在同一台换热器内就形成了2个温度不同的区域。在温度较高的区域管子热膨胀量大、蠕变变形量也大。温度 低区域的管子则限制高温区域管子的膨胀,最初因温度高的管子较少,每根管子所受的压力很大,使得这一部分管子弯曲变形。随着温度高的管子增多,每根管子所 受压力变小,但温度低的区域每根管子的拉力增大,最终达到力的平衡。至于折流挡板的形变则是因为管束形变所致。
2、对策
1)严格控制原料油成分
目前,对于焦化蜡油中的焦粉尚无有效的脱除方法。因此在保证焦化装置平稳生产的前提下,应严格控制焦化蜡油中的焦粉含量。上游的常减压装置要控制好适 宜的总拔,不要片面追求过高的拔出率而使部分减压渣油馏分进入减四线,造成催化原料过重,影响催化原料性质。对于多年的罐底原料要作杂质等成分分析,各项 指标均合格的情况下才能送催化做原料,防止其中杂质过多而影响装置的正常生产。!焦化蜡油进行加氢或糠醛溶剂抽提后,再送催化装置做原料,以此改变原料性 质。锦西炼油化工总厂新上一套15万t/a的焦化蜡油加氢装置,焦化蜡油经加氢后再送催化做原料,其性质大为改观。
2)提高原料在换热器壳程的线速
保持适宜的原料处理量,防止处理量过小影响线速度。由于H-209/1,2是并联,在满足生产需要的前提下,尽可能将换-209/1,2中的1台切 除,那么线速就可提高近一倍。另外应控制油浆从分馏塔底的抽出温度不高于365℃,在生产允许的情况下,尽量保证分馏塔底温度低于360℃,以降低换热后 的原料温度,防止原料发生热裂化和缩合生焦等反应。
3)防止管束变形
一般地,有两种原因可能导致原料-油浆换热器管束变形。一是换热器壳程结焦。二是管程堵塞,堵塞的管子内的油浆温度接近于壳程的原料温度160℃,而 未堵塞的管子内的油浆温度为370℃,这样就造成管束与管束之间存在温差。堵塞的管子温度低,未堵塞管子温度高,两部分管子自由热膨胀量不同。造成未堵塞 管子大多数都发生严重弯曲变形。堵塞管子因受拉而部分与管板脱开,发生泄漏。
为防止管束变形,除控制原料成分满足生产工艺要求外,还采取了以下措施:
避免人为堵死管束,在换热器检修时,凡有窜漏和渗透的管束均予以更换。改善工艺操作,减少分馏油浆循环系统生焦,采用高效旋风分离器,减少催化剂随油 气的带出量,进而降低油浆中的催化剂浓度;油浆泵出口管线加两组过滤器,切换使用,定期清理;在分馏塔底加1.2m高的圆筒型筛孔过滤器,防止焦块带入油 浆循环系统;油浆泵出口加注阻垢剂,减缓和防止该系统结垢、结焦;严格控制分馏塔底液相温度不大于365℃;在综合经济效益允许的情况下,可以适当外甩一 定比例的油浆;控制油浆的循环量不低于150t/h,油浆在流经管线和冷换设备时流速不低于1.3m/s,在分馏塔底的停留时间不大于5min,循环油浆 在流经蒸汽发生器时一般尽量多走冷流少走热流,以提高油浆在管程的线速;搞好平稳操作,减少工艺波动。
通过采取以上防范措施,原料-油浆换热器结焦及管束变形得以减缓和控制。1998年第2季度装置大修时打开此换热器检查,没有发现壳程结焦及管束、管板变形,证明上述技术措施换热设备厂家优质供应兴宁换热器板式换热器管式换热器钎焊式换热器空气散热器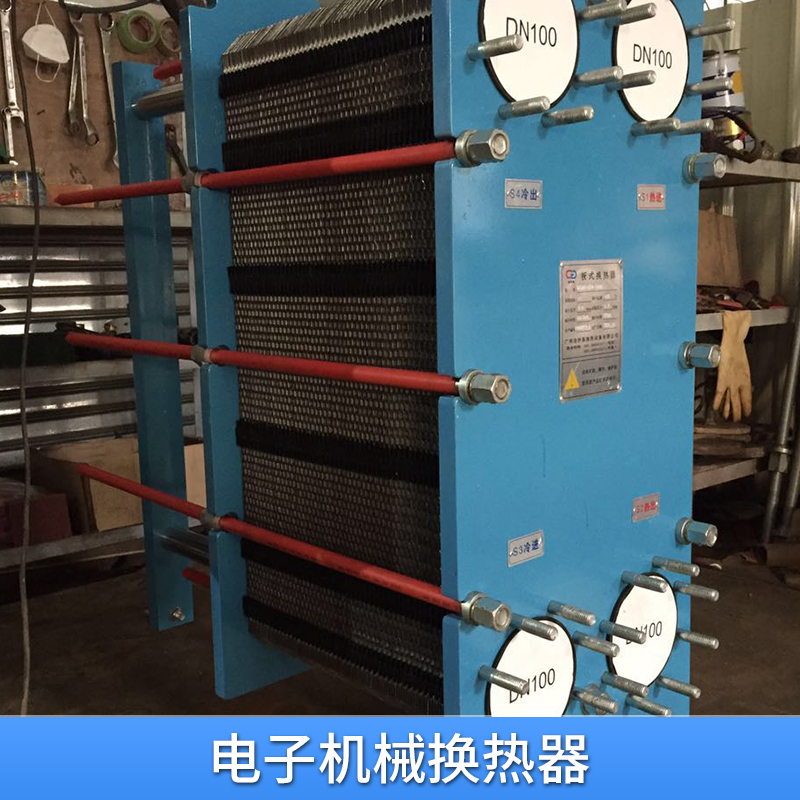
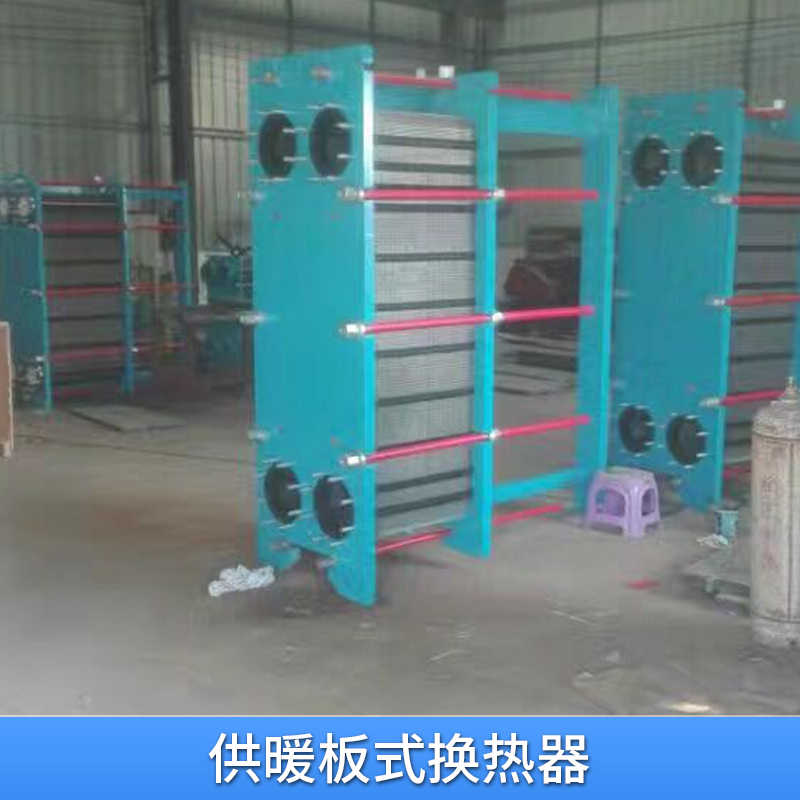
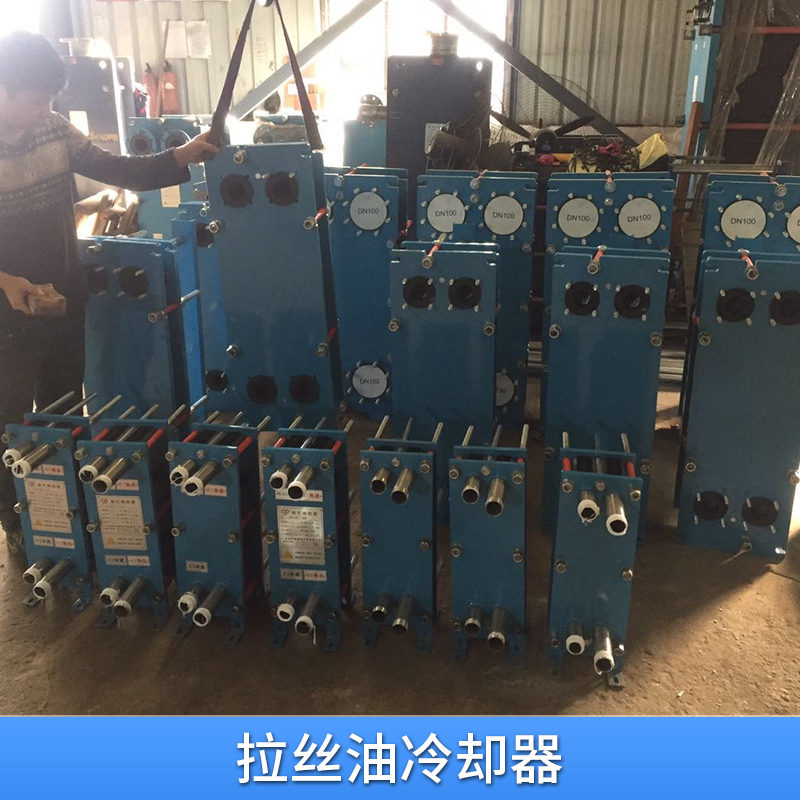
1、原因分析
1)壳程结焦
原料-油浆换热器结焦的焦层呈黑褐色片状,厚度平均3~5mm,质地疏松,用手一捏即碎,肉眼观察断层很容易看到结焦物的两侧发亮,而内部色泽较暗。 两侧闪亮的薄层是在换热器结焦缩合后形成的产物,其中可燃物部分占60.1,系焦化蜡油中的焦粉和在换热器缩合后形成的焦碳,剩余部分为不可燃烧的无机物 等杂质。
从理论上讲,原料系统在进提升管之前不可能结焦,原料经过换-201/1,2、换-204/1,2、换-206,最后到换-209/1,2换热,其终 温不高于260℃,根本达不到缩合生焦的温度需要。因此认为:原料油浆换热器壳程结焦,主要与原料中的焦粉、油浆换热后的温度及原料在壳程的线速有关。
原料中焦粉多近年来该装置原料逐年变重、变差,特别是原料中的焦粉因无有效的脱除方法被大量带入催化(催化法勘测离子电池阳极装置中的材料)装置,以 1997年为例,共加工辽河焦化蜡油216000t,其中的焦粉按0.35计,则全年流经原料-油浆换热器壳程的焦粉量高达756t,因此遇适宜的条件, 就可能在壳程出现沉积。
线速低装置处理量若按90t/h计,则原料流经此换热器的线速仅0.11m/s,是原料流经所有换热器中线速最低的,见。
原料以低速流经该换热器时就可能有一小部分焦粉沉积在换热器的底部、管束的表面及折流挡板的两侧,随着时间的推移越聚越多,于是在某个区域形成死区,即不流动区。
死区温度高由于原料是与分馏塔底抽出的370℃高温油浆换热,一旦形成不流动区,该区域的原料换热后的温度便接近或达到油浆的温度,而具备热裂化等化 学反应的条件,进而发生热裂化等结焦缩合反应,与沉积的焦粉粘合在一起形成结焦物。原料中焦粉含量和杂质越多,在壳程的线速越低,不流动区域越多,壳程结 焦就可能越严重。另外,当原料中重金属含量增加时,镍的脱氢活性对脱氢缩合反应会起到催化作用,加速焦炭的形成。再一方面,由于常减压采取深拔措施后,使 得直馏蜡油性质明显变劣,氢含量只有12.1,也使结焦倾向增大。
值得说明的是,从原料系统打开的其它换热器壳程均未发现有类似的结焦物,这主要是因为其它原料换热器线速高,焦粉等不易沉积,同时换热后原料温度低,达不到发生缩合等反应应具备的条件。
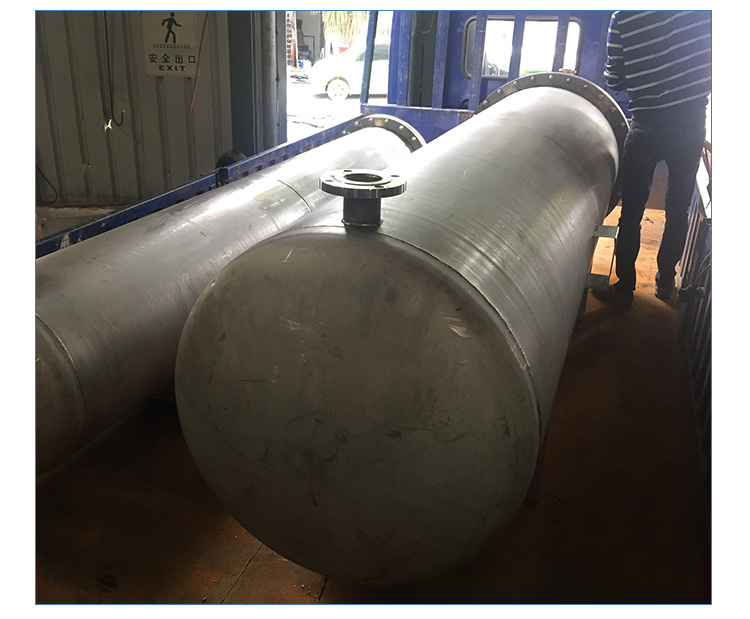
热交换器构件问题型焦结和形变应对
2)管束变形
在换热器管束检修清洗过程中,看到有许多管子弯曲变形,尤以外围管束最为严重,变形管束约占2/5,但管子均畅通。检查中还发现折流挡板不同程度变形。
如前所述,原料中的焦粉及其它杂质过多,线速较低易形成结焦,结焦形成的不流动区导致该区域管束内外温度趋近相同,即接近油浆的温度365℃。而流动 区壳程原料油的温度一般由70℃升至200℃,于是在同一台换热器内就形成了2个温度不同的区域。在温度较高的区域管子热膨胀量大、蠕变变形量也大。温度 低区域的管子则限制高温区域管子的膨胀,最初因温度高的管子较少,每根管子所受的压力很大,使得这一部分管子弯曲变形。随着温度高的管子增多,每根管子所 受压力变小,但温度低的区域每根管子的拉力增大,最终达到力的平衡。至于折流挡板的形变则是因为管束形变所致。
2、对策
1)严格控制原料油成分
目前,对于焦化蜡油中的焦粉尚无有效的脱除方法。因此在保证焦化装置平稳生产的前提下,应严格控制焦化蜡油中的焦粉含量。上游的常减压装置要控制好适 宜的总拔,不要片面追求过高的拔出率而使部分减压渣油馏分进入减四线,造成催化原料过重,影响催化原料性质。对于多年的罐底原料要作杂质等成分分析,各项 指标均合格的情况下才能送催化做原料,防止其中杂质过多而影响装置的正常生产。!焦化蜡油进行加氢或糠醛溶剂抽提后,再送催化装置做原料,以此改变原料性 质。锦西炼油化工总厂新上一套15万t/a的焦化蜡油加氢装置,焦化蜡油经加氢后再送催化做原料,其性质大为改观。
2)提高原料在换热器壳程的线速
保持适宜的原料处理量,防止处理量过小影响线速度。由于H-209/1,2是并联,在满足生产需要的前提下,尽可能将换-209/1,2中的1台切 除,那么线速就可提高近一倍。另外应控制油浆从分馏塔底的抽出温度不高于365℃,在生产允许的情况下,尽量保证分馏塔底温度低于360℃,以降低换热后 的原料温度,防止原料发生热裂化和缩合生焦等反应。
3)防止管束变形
一般地,有两种原因可能导致原料-油浆换热器管束变形。一是换热器壳程结焦。二是管程堵塞,堵塞的管子内的油浆温度接近于壳程的原料温度160℃,而 未堵塞的管子内的油浆温度为370℃,这样就造成管束与管束之间存在温差。堵塞的管子温度低,未堵塞管子温度高,两部分管子自由热膨胀量不同。造成未堵塞 管子大多数都发生严重弯曲变形。堵塞管子因受拉而部分与管板脱开,发生泄漏。
为防止管束变形,除控制原料成分满足生产工艺要求外,还采取了以下措施:
避免人为堵死管束,在换热器检修时,凡有窜漏和渗透的管束均予以更换。改善工艺操作,减少分馏油浆循环系统生焦,采用高效旋风分离器,减少催化剂随油 气的带出量,进而降低油浆中的催化剂浓度;油浆泵出口管线加两组过滤器,切换使用,定期清理;在分馏塔底加1.2m高的圆筒型筛孔过滤器,防止焦块带入油 浆循环系统;油浆泵出口加注阻垢剂,减缓和防止该系统结垢、结焦;严格控制分馏塔底液相温度不大于365℃;在综合经济效益允许的情况下,可以适当外甩一 定比例的油浆;控制油浆的循环量不低于150t/h,油浆在流经管线和冷换设备时流速不低于1.3m/s,在分馏塔底的停留时间不大于5min,循环油浆 在流经蒸汽发生器时一般尽量多走冷流少走热流,以提高油浆在管程的线速;搞好平稳操作,减少工艺波动。
通过采取以上防范措施,原料-油浆换热器结焦及管束变形得以减缓和控制。1998年第2季度装置大修时打开此换热器检查,没有发现壳程结焦及管束、管板变形,证明上述技术措施换热设备厂家优质供应兴宁换热器板式换热器管式换热器钎焊式换热器空气散热器
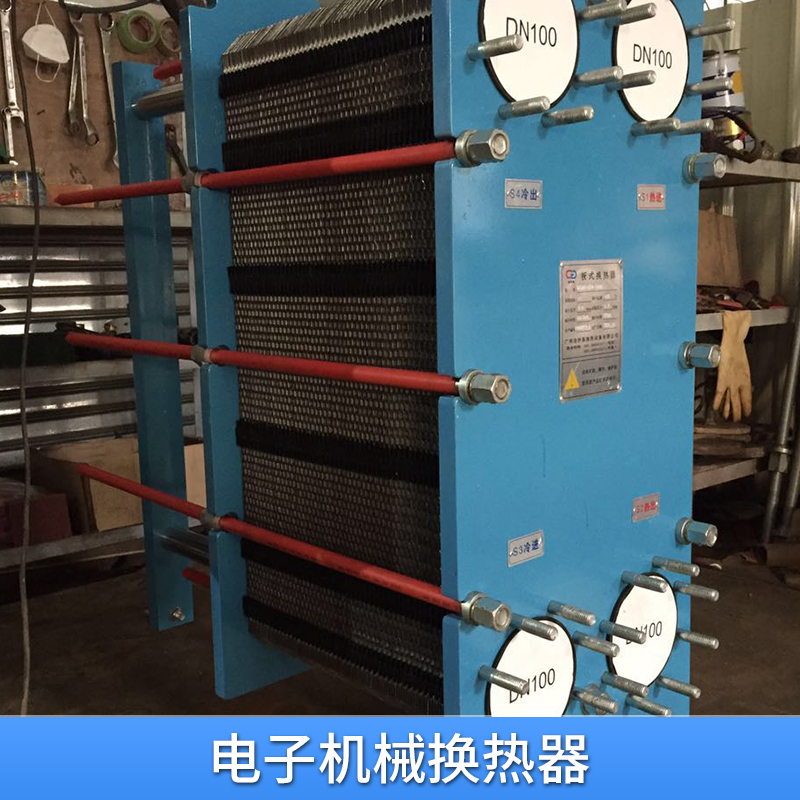
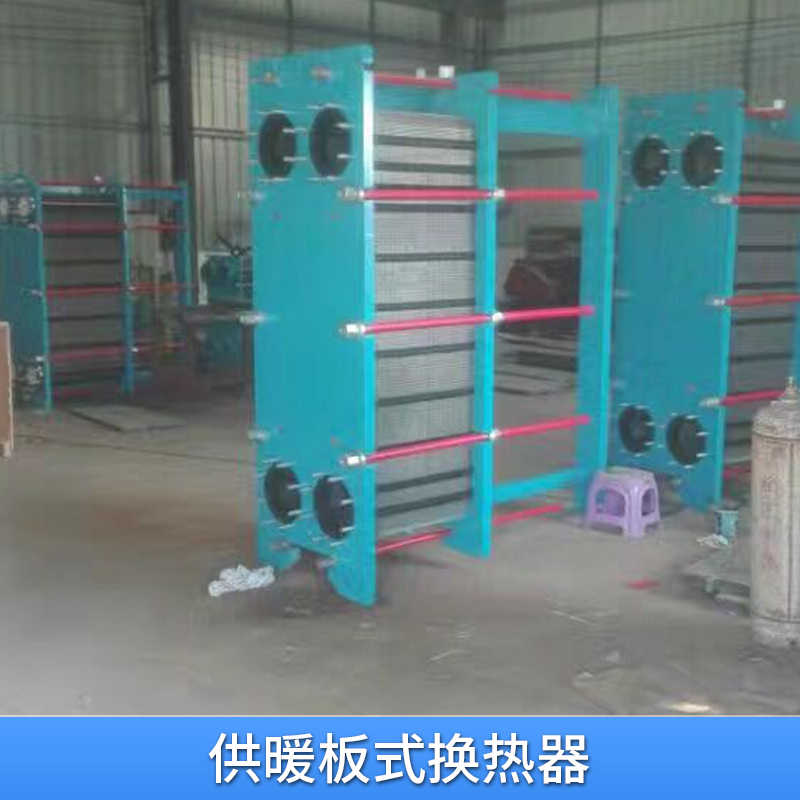
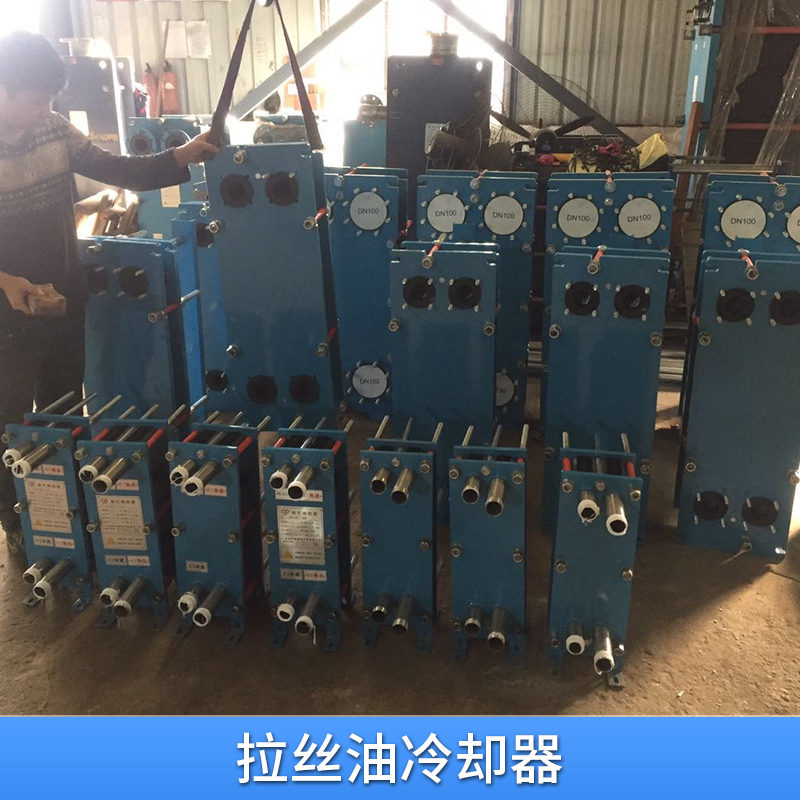
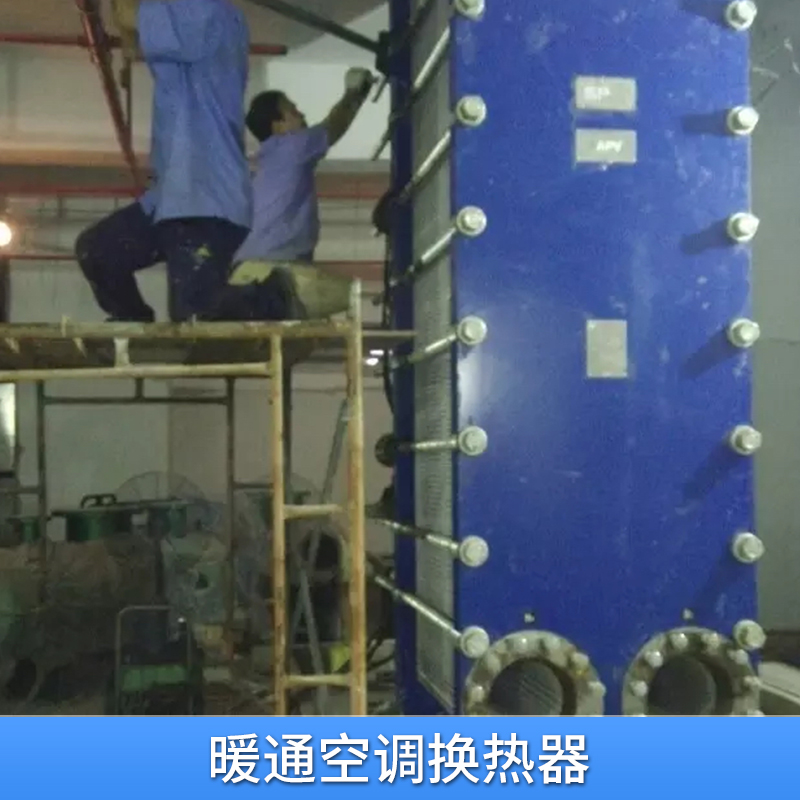
1)壳程结焦
原料-油浆换热器结焦的焦层呈黑褐色片状,厚度平均3~5mm,质地疏松,用手一捏即碎,肉眼观察断层很容易看到结焦物的两侧发亮,而内部色泽较暗。 两侧闪亮的薄层是在换热器结焦缩合后形成的产物,其中可燃物部分占60.1,系焦化蜡油中的焦粉和在换热器缩合后形成的焦碳,剩余部分为不可燃烧的无机物 等杂质。
从理论上讲,原料系统在进提升管之前不可能结焦,原料经过换-201/1,2、换-204/1,2、换-206,最后到换-209/1,2换热,其终 温不高于260℃,根本达不到缩合生焦的温度需要。因此认为:原料油浆换热器壳程结焦,主要与原料中的焦粉、油浆换热后的温度及原料在壳程的线速有关。
原料中焦粉多近年来该装置原料逐年变重、变差,特别是原料中的焦粉因无有效的脱除方法被大量带入催化(催化法勘测离子电池阳极装置中的材料)装置,以 1997年为例,共加工辽河焦化蜡油216000t,其中的焦粉按0.35计,则全年流经原料-油浆换热器壳程的焦粉量高达756t,因此遇适宜的条件, 就可能在壳程出现沉积。
线速低装置处理量若按90t/h计,则原料流经此换热器的线速仅0.11m/s,是原料流经所有换热器中线速最低的,见。
原料以低速流经该换热器时就可能有一小部分焦粉沉积在换热器的底部、管束的表面及折流挡板的两侧,随着时间的推移越聚越多,于是在某个区域形成死区,即不流动区。
死区温度高由于原料是与分馏塔底抽出的370℃高温油浆换热,一旦形成不流动区,该区域的原料换热后的温度便接近或达到油浆的温度,而具备热裂化等化 学反应的条件,进而发生热裂化等结焦缩合反应,与沉积的焦粉粘合在一起形成结焦物。原料中焦粉含量和杂质越多,在壳程的线速越低,不流动区域越多,壳程结 焦就可能越严重。另外,当原料中重金属含量增加时,镍的脱氢活性对脱氢缩合反应会起到催化作用,加速焦炭的形成。再一方面,由于常减压采取深拔措施后,使 得直馏蜡油性质明显变劣,氢含量只有12.1,也使结焦倾向增大。
值得说明的是,从原料系统打开的其它换热器壳程均未发现有类似的结焦物,这主要是因为其它原料换热器线速高,焦粉等不易沉积,同时换热后原料温度低,达不到发生缩合等反应应具备的条件。
相关产品推荐